在化学工业中,气固相催化反应是重要的一环,广泛应用于石化、化学合成、食品饮料加工以及环保等领域。传统的气固相催化反应装置,如单通道催化反应器,虽然在一定程度上满足了工业生产的需求,但在催化剂评价和筛选过程中,效率低下的问题一直困扰着科研人员。为了提高催化剂评价的效率,多通道催化反应装置应运而生。本文将详细探讨设计、应用及其在实际生产中的重要意义。
气固相多通道催化反应装置的设计初衷,在于解决传统单通道反应器在催化剂筛选和评价上的不足。传统的单通道反应器一次只能对一个催化剂进行评价,这使得科研人员在面对大量催化剂样本时,需要投入大量的人力、时间和资源。为了提高效率,多通道催化反应装置被开发出来。这种装置通过增加反应通道的数量,实现了对多个催化剂的同时评价,大大提高了工作效率。
在实际应用中,通常采用四通道或更多通道的设计,以适应大规模催化剂筛选的需求。每个通道都可以独立控制反应条件,如温度、压力和气体流量,从而确保每个催化剂样本都能在较佳的反应条件下进行评价。此外,该装置还配备的自动控制系统和数据采集系统,能够实时监控反应过程中的各种参数,自动记录实验数据,大大提高了实验的可靠性。
气固相多通道催化反应装置的核心部件是反应器,它通常由石英管等耐高温、耐腐蚀的材料制成。石英管反应器具有小管径的特点,这使得反应物在反应器内的停留时间更短,反应速度更快,同时减少了催化剂的用量。此外,小管径反应器还适合做动力学表征分析,能够提供更加准确的反应动力学数据。
在催化剂评价过程中,能够同时处理多个催化剂样本,通过对比不同催化剂在相同反应条件下的催化效果,可以更加直观地评估催化剂的优劣。这种并行处理的方式不仅提高了工作效率,还降低了实验误差,使得催化剂评价的结果更加可靠。
除了在催化剂评价方面的应用,在工业生产中也具有广泛的应用前景。在石化行业中,该装置可以用于催化裂化、脱硫等过程的优化,提高石油的加工效率和产物质量。在化学行业中,该装置可以用于生产氢气等燃料和化学合成过程,降低生产成本和环境污染。在食品饮料行业中,该装置可以用于生产含有特定催化剂的食品饮料,提高产物的质量和口感。在环保领域中,该装置可以用于工业废气的治理,通过催化反应降低废气中污染物的浓度,减少对环境的污染。
此外,气固相多通道催化反应装置还可以用于催化反应动力学研究、催化剂合成参数优化等方面。通过改变反应条件,如温度、压力和反应物浓度,可以研究催化反应的速率和机理,为催化剂的改进和优化提供理论依据。同时,该装置还可以用于催化剂活性及寿命的考察,为催化剂的长期使用和性能稳定性提供实验支持。
在设计和制造时,需要考虑多种因素,如反应器的材料选择、通道数量的确定、自动控制系统的设计等。这些因素直接影响到装置的性能和使用效果。因此,在设计和制造过程中,需要充分考虑实际需求和操作条件,选择合适的材料和设备,确保装置的稳定性和可靠性。
总之,气固相多通道催化反应装置作为一种新型的催化反应设备,在催化剂评价、工业生产以及科研研究中具有广泛的应用前景。它通过提高催化剂评价的效率,降低了生产成本和环境污染,推动了化学工业的可持续发展。随着科技的进步和工业化进程的加速,将会在未来的化学工业中发挥更加重要的作用。
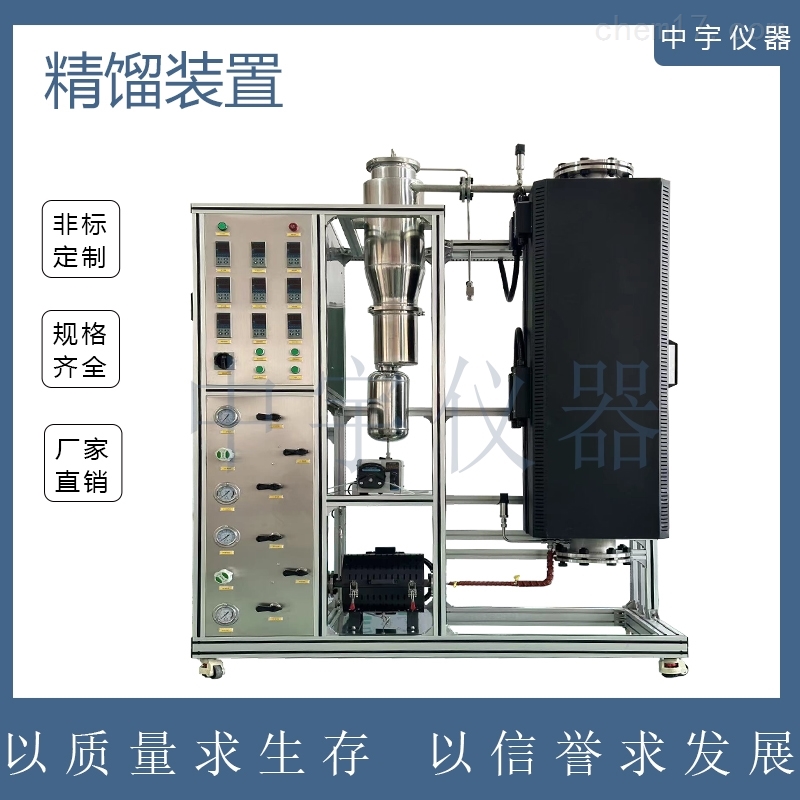